ことラボ・レポート
《MF-Tokyo2023》が開催された
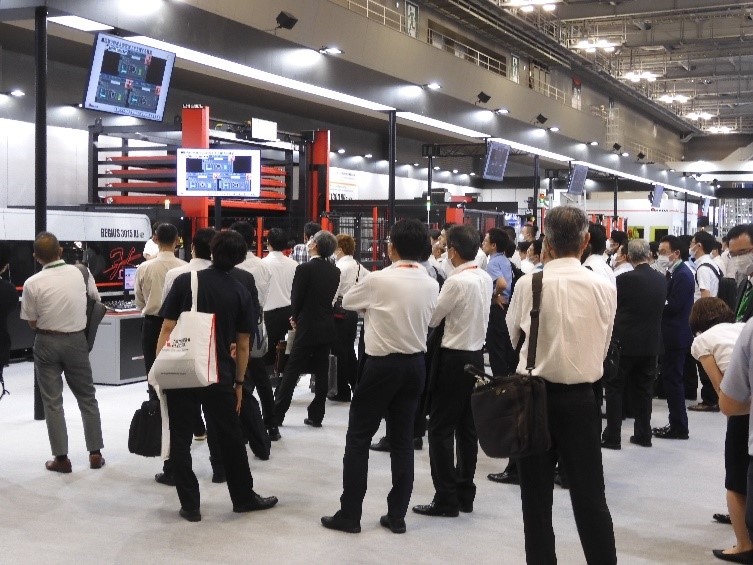
《MF-Tokyo2023》概観
7月 12 日から 15 日まで、東京ビッグサイト東4~8ホールで第7回 プレス・板金・フォーミング展《MF-Tokyo2023》が開催された。会期中の東京の最高気温は 35 ℃を筆頭に「不要な外出を控えるように」との警報が連日出ていたので不要か否かを考えなければならない状況だった。それでも展示会場は適度のエアコンが効いていたので、太陽が傾く夕方まで会場に残ろうか迷ったほどだ。
《MF-Tokyo》は「プレス・板金・フォーミング展」との別名を持っているように3分野の共同展で一般社団法人日本鍛圧機械工業会と日刊工業新聞が共同開催している。今回は「人と地球に優しい技術、確かな未来のために」をテーマに、233 社・団体、1,677 小間の規模で開催され、ビッグサイトの東4~8ホール、5ホールを使うのは過去最大だ。小間図面もプレス機械・周辺機器装置の「青色ゾーン」、フォーミングマシン・ねじ・ばね・パイプ機械・周辺機器装置の「黄色ゾーン」、板金機械・周辺機器装置の「緑色ゾーン」に分けられていた。
世界の工業会で「切削系機械」=工作機械と「成形系機械」=鍛圧機械に分けているのは日本だけのようだ。というより各国の工業会のあり様をみると、ドイツでもイタリアでもスイスでも、工業会は一つで、イタリアのUCIMUは正確に訳すると工作機械・ロボット・自動化機器工業会と欲張っている。しかし日本でこの分野を管轄するのが経済産業省の製造産業局「産業機械課」と「素形材産業室」に分かれている。その影響か、ものづくり関連の団体が少し多くなったのかもしれない。
それはさておき《MF-Tokyo》は、5ホールを使ったことにより、通路はゆったりとして外は暑くても中の涼しさはありがたかった。
《MF-Tokyo2023》動員数の記録
《MF-Tokyo》への提言
(1)入口のワゴンで配布されていた資料
企業が個社として開催するいわゆる“プライベートショー”は各社の工夫が優先されるが、工業会という“一般社団法人”が主催する展示会で、「公式ガイドブック」がなかったことに驚いた。プレス登録する際に確認すると、JIMTOFなどで制作される「公式ガイドブック」はなく、入り口のワゴンで配布している資料を利用するように、と。以下がその資料だ。
①《MF-Tokyo 2023》会場MAP~A4版×3の両面印刷
小間図面と出展者一覧(表面)と期間中のセミナー・講演会案内
②日刊工業新聞社「プレス技術」「型技術」合同編集版
特別誌上展「MF-Tokyo 2023」第7回プレス・板金・フォーミング展 会場MAP付き
③日刊工業新聞 7月5日 第2部 MF-Tokyo2023 特集
④日刊工業新聞 7月 12 日 開会初日版
⑤一般社団法人 日本金属プレス工業協会 特別寄稿「わが社の一押し情報」―賛助会員 30 社
本展全体を紹介する拡がりを持っているのは①の会場MAPだけ。他は広告出稿企業だけの紹介(②③④)、他の企画の転用(⑤)で、主催者が広報予算を使って来場者に配布する「公式ガイドブック」は見当たらなかった。会場一番奥のプレスルームにあったのか、疑問の多い運営だった。
共同主催者の日刊工業新聞はともかく、公益団体である一般社団法人 日本鍛圧機械工業会は、全出展者のリストや出展商品をまとめた「公式ガイドブック」を発行して、鍛圧機械業界の記録となる資料を作成するべきだと思う。展示会の規模がJIMTOFより小さいが、そうしないと鍛圧機械産業の将来を明るく展望できない。
(2)貧弱なプレス対応~会場撮影のモラル
プレス受付時に渡され資料の表紙に「展示場内原則撮影禁止」という注意書きがあった。この見出しが効いているのか、会場内の様子を撮影していた時に、小間から飛び出してきた出展者の若者が「いま撮ったでしょ?ここは撮影禁止です」と抗議してきた。私は撮影した写真を見せると画面の端に写り込んでいた。消しますか?と確認すると、すこし狼狽えて「ええ」というので削除した。
取材する者の常識として、小間の撮影をするときは、出展者に確認しているが、会場の様子を伝えるための撮影に「ウチが映った」と抗議されたのは初めてだ。展示会とは何だろう? 私は、メディアに配布された言葉足らずの「取材の皆様へ」に原因があると思う。
欧米の展示会では、写真撮影に大変な努力がいる。ある工作機械メーカーの先達から、ミラノEMOでは入口ゲートでカメラは没収され一時預かりだった、と聞いた。「へぇ」と思ったが、その時は取られなかった。会場に入り、撮影を始めたら「ダメだ。あっちへ行け」(と多分イタリア語で)追い払われた経験がある。1990 年代の中頃のことだ。日本人を中心としたアジア勢が、欧米の意匠性の高い機械のデザインなどを勝手に真似している、と非難されていた頃だ。主催者側の配慮に欠けた言葉遣いに過剰に反応した出展者の誤解から昔の経験を思いだした。
(3)4ホールから7ホールへ
トミタの小粋な新商品
配布されていた小間図面に従い東4ホールから会場を見たが、商社のトミタ(東日本営業部本社営業二課・課長代理:斎藤基宏、同:柄澤宏輔)が面白い新商品を展示していた。
同社は同展示会第1回からの常連。オルトリングハウスのクラッチを前面に出していたが注目したのは後ろに展示していたFDX社(FDX Fluid Dynamix GmbH)の「OsciJet nozzle」。流体の噴出口に取り付ける。内部に“仕掛け”があり、落下する流体に内部のコマが動かされ噴射口から液体を四方八方に“散水”する。リボンをくるくる回すように渦巻き状に散布する。動力は不要で液体の落下エネルギーだけで効果を生む、カーボンニュートラル時代に相応しい。
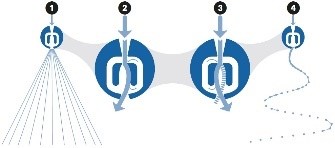
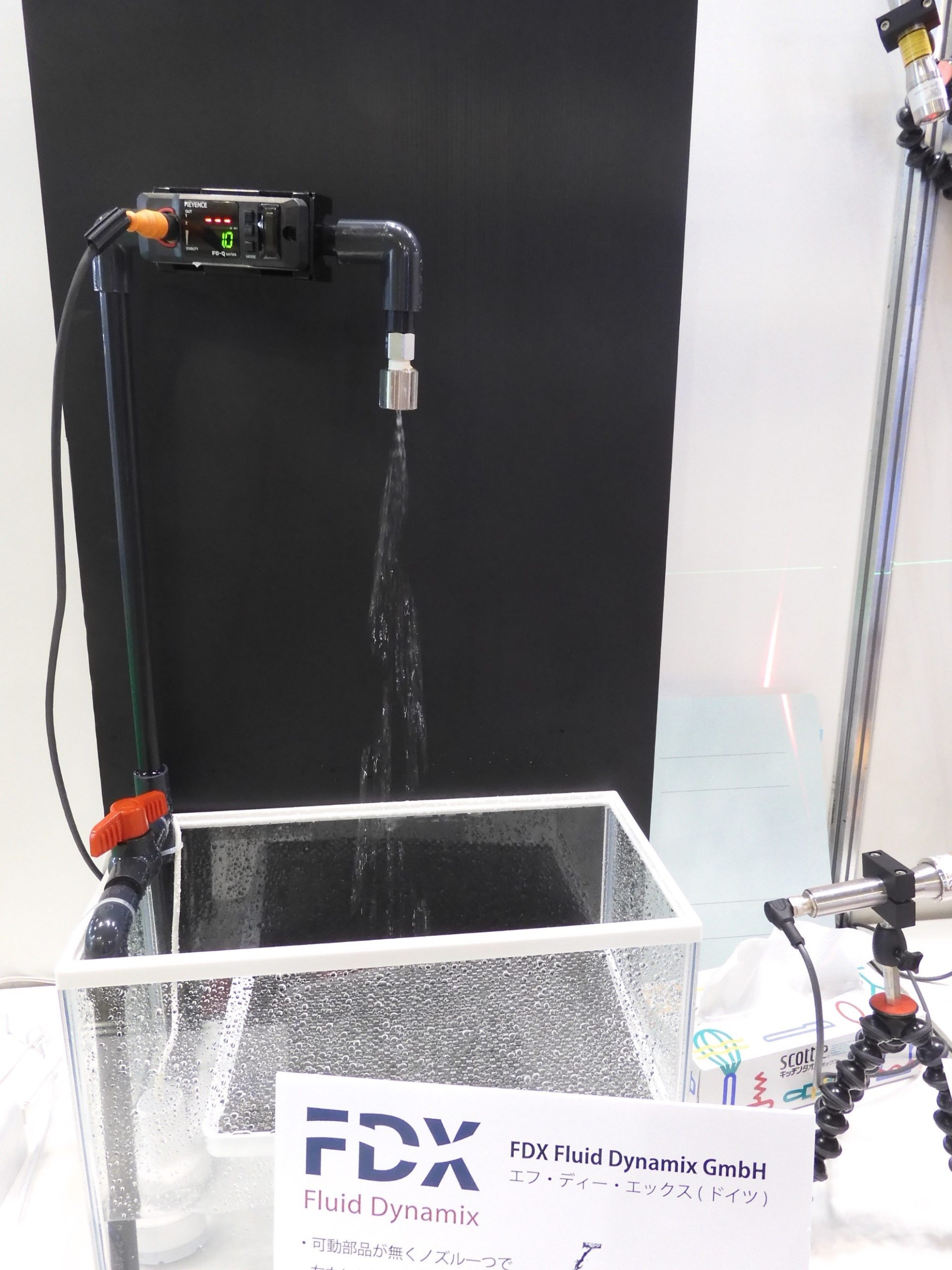
榎本機工
国内で唯一のスクリュープレスのメーカー榎本機工(榎本良夫社長)の鮮やかな緑色のプレス機が目に飛び込んで来た。ねじの回転する力で加圧するスクリュープレスは、スライドを加減速できる機構で鍛圧加工のひとつのジャンルを形成している。
写真にワークのハンドリング用多関節ロボットが映り込んでいるが、榎本社長は「いまではロッボトとセットにする例が多くなり、そのセッティングを自社で行えるようにエンジニアリング力を強化している」。そのため年末に毎年、ロボットを使った社内コンテストを開いている。「ロボットをつけての納入例が多くなり、そのエンジニアリングを社外に依存するとコストも納期も増えてしまう。自社で対応するには、社員がロボットを使いこなすようにならねば」と社内コンテストの趣旨を語る。今年のテーマは「塗装(ペンキ塗り)」という。「人がやりたがらないが技術的には難しい」とのこと。ロボットを“道具”として使いこなそうという発想こそ、何でもAI時代に必要な姿勢だと感じた。
また榎本機工は、以前から写真のような模型を小間内に展示している。スクリュープレスの構造を判り易く説明している。プレス機械は剛性を確保するために重量が大きい。展示場の耐荷重が低いと、機械本体を展示できないこともある。このような可愛らしい模型が、いかつい鍛圧機械に親しみを感じているのは私だけではないと思う。
アイダエンジニアリング(鈴木利彦社長)の実機出展は6年ぶりという。今回の呼び物は「プレスラインのトータルソリューション」だ。プレス機本体の前後を、①アンコイラ「ADU-5-600E」、②Sループ装置「ASV-600」、③高速フィーダー「ADF-600」、④転積装置「ARM-30」、⑤サーボ駆動式スクラップカッター「ASC-600」まで、プレス本体を含むすべてをAIDAがサポートする商品を揃えた。同社は、そればかりかサーボプレスに使う、低速回転高トルクのサーボモータそのものも内製している。
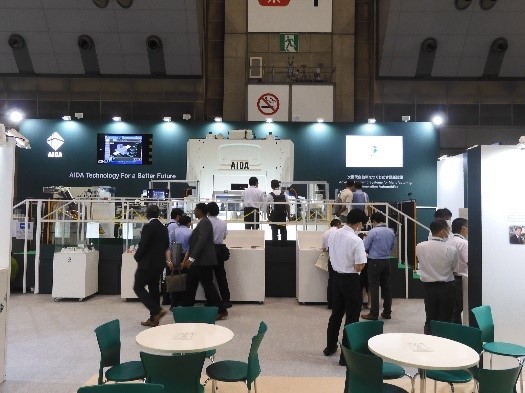
前面に「SDE2025lⅢ」「SDE8081iⅢ」2台の合計3台のプレス機を2台のハンドリングロボットがワークの受け渡しをするシステムを展示していた。また小間内に入ると「DSEW1613iⅢ」「SDE2017iⅢ」が並び、ローダを付したシステムを展示していた。榎本機工で聞いたようにロボットの展示が目に付いた。
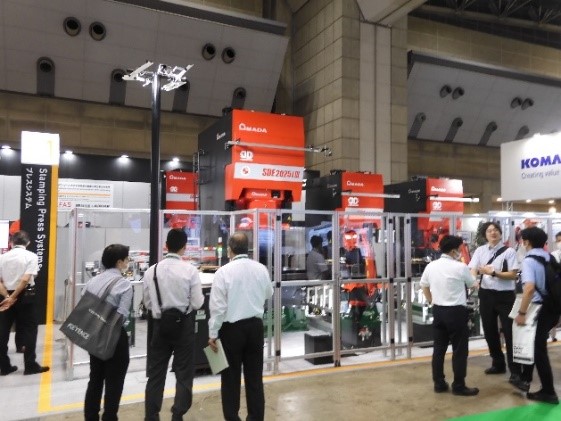
ここでもハンドリングロボットが「SERVO HIF 200」をハンドリングロボットがサポートするシステム展示をしていた。が注目したのは、リニューアル機「OBS80」の展示。日本の産業界では「新製品を売るべきだ」というのが、金科玉条の真理だったのだろう。「オーバーホール」や「レトロフィット」さらに「工具再研磨」には注目が集まらない。すでに製造現場で活躍している“現役”のアイテムに、復活のエネルギーを注力することに、もっと積極的であるべきだと思っていた。展示されていた最先端のシステムよりも、小間の奥に展示されていた「リニューアル機」に「SDGs対応」と大書きしていれば、注目を集めたのではないか。
社名から伺えるように鍛圧機械業界でユニークな魅力を発揮する放電精密加工研究所(村田力社長)は、スライドをスクリュータイプの直動ユニットで上下動させるプレス機「ZENFormer」で存在感を発揮している。機械本体の製造販売、金型や部品加工、部品生産システムなど手広く手掛けている。芸達者な中堅企業だが、持っている可能性は高い企業だ。
三起精工
北関東は戦前の中島飛行機の遺伝子が残る、製造業の集中している地区だが、足利市にある三起精工(大関敏也代表取締役)もその中の1社で、油圧プレスメーカーとして手堅く事業展開している。自動車産業が主要ユーザーで、車体系の仕事であるためにいまのEV問題の影響は薄い。また堅実な仕事が評価されてリピート率が高いのがちょっとした自慢だ。
反転式ダイスポッティングプレス、トライアウトプレス、トリミングプレス、成形プレス、ヘミングプレス、ホットプレス、高速深絞りプレスなど多彩な商品展開をしている。
油圧プレスは、ストロークの全工程で加圧力を発生できる特性を生かして、メカ式プレスにはできない多芸な仕事をこなせる。これからの活躍が楽しみな企業のひとつだ。
実機の展示が少ない
ここであることに気がついた。三起精工のように機械展示の無い出展者が多いことだ。住友重機械工業や栗本鐵工所など機械が大きすぎるメーカーもあるが、エイチアンドエフ、アミノ、川崎油工、森鉄工など小間内に実機を展示できるはずだ。
しかしプレスは金型がついて仕事をする生産設備だ。そしてその金型はユーザーが作成するノウハウの塊だ。これはマシニングセンタに工具がついていない、というレベルの問題ではない。プレス機を展示会に出しても無駄だという声はいまでもある。しかし機械を展示しなかった出展者は、この新型コロナのリモート時代に、新しい販売促進手法を考案したのだろうか? 疑問がはれないまま、黄色ゾーン、緑ゾーンに向かった。
(4)フォーミングマシンなどの黄色ゾーンへ
この分野は“産業機械”として位置づけられることが多いが、ばねやねじなどの身近な部品の高速に精密に製造する技術が溢れている。世界で初めてコンピュータ制御のばね成形機を開発した板屋製作所が目を引いた。その「ばね成形機」では以前、横浜にあったドイツの企業が“なるほど”と納得できる機械を輸入していた。それがいくつかの変遷を経て東7ホールの伊藤忠マシンテクノスに顔を出していた。同社が扱う数ある商材のひとつとしてパネル展示をしていた。ドイツのビーラー社である。線材を高速で成形していくが、以前はコンピュータを使わずカムによる制御で、トラブルが少なく、トラブってもマニュアルに従って辿っていくと故障の場所が明らかになり、その部品を特定してドイツ本社に連絡すると、翌日には航空便でその部品が届き、ユーザーが自分で直す、という仕組みだった。いまは更に進化しているようだが、取材は改めて参上することにした。
ニッセーとヘガネスジャパン
「まだ削りますか」という強烈なコピーを展開するニッセー(新仏克利社長)は、同社の転造技術を駆使して、緩まないねじ「パーフェクト・ロック・ボルト(PLBv2)」の販売に注力している。PLBv2はピッチの異なるボルトに二種のナットで締め付けることで発生する摩擦で緩みを防ぐ。ニッセーは、それを自社開発したCNC制御の転造技術で製造している。ニッセーは第9回「ものづくり日本大賞」の経済産業大臣賞を今年2月に受賞している。「社内を、従来の生産財としての転造技術を製造販売する部門とPLBv2の拡販に専心する部門に分け、前者を新社長の新仏克利に、後者を新仏利仲会長と私がタスクフォースで担当することになった」と深山宗谷専務取締役。
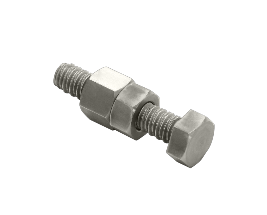
ヘガネスジャパン
ニッセーの小間内に同居していたのはスウェーデンのヘガネス社の日本法人。「金属粉の世界的リーダー」を自認するだけあり、いくつかの事例を聞き及んでいる。同社の鉄粉を焼結してニッセーの転造技術で“圧密転造”で成形した歯車が、自動車メーカーで使われている。生産性向上を模索する企業には福音かもしれない。(5)東6ホールから東7ホールの板金機械ゾーンへ
東6ホールから7ホールに行くには一度展示棟を出て、車道を渡りさらに奥の展示棟に行かなければならない。しかし、東7ホールに入ると、目の前にアマダとトルンプの板金業界の両横綱が待ち構えていた。東京ビッグサイトの正面入口から東ホールへの動く歩道を超えて東ホールの端から端まで通り抜けやっとたどり着いての東7ホールだが、アマダのブースはどこよりも人で溢れていた。本稿初めの写真も東7ホールのアマダブースだ。さすがにアマダの動員力と感心したが、世界市場でアマダと戦うトルンプは、平行四辺形のブースで使いづらそう。奥に三菱電機・村田機械連合、ヤマザキマザック、サルバニーニなどの主要企業が小間を構えていたが、板金分野に関しては改めて取材活動を行う予定です。
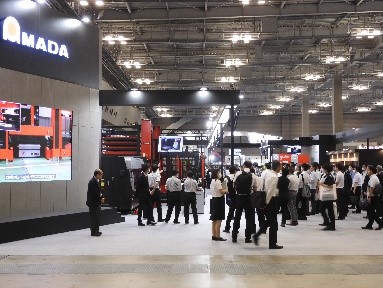
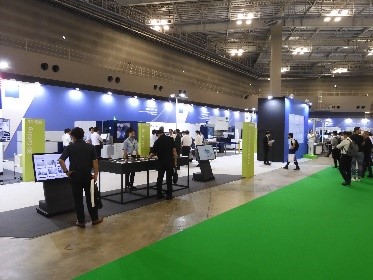