技術者のバトン
ニットー 藤澤 秀行 社長/ インタビュー
株式会社ニットー
代表取締役
藤澤 秀行
1973 年3月 26 日生まれ 神奈川県出身
1997 年 11 月 入社
家族構成:妻 長男 長女 次男
趣味:マラソン キャンプ
Q.御社(ニットー)について教えてください。
当社の創業は 1967 年 9 月です。当時、私の父(現会長)が神奈川県横浜市磯子区にて日東工業としてスタートしました。最初は、金型製造を中心とした金型メーカーとして始めており、創業者である父のモットーは「いい仕事をすれば、必ず次のいい仕事につながる」という考えのもとでものづくりを行っていました。
父自身も常に新しいものに興味を持ち、吸収し続けるタイプでしたので、そんな姿も私にとってものづくりの現場が魅力的に映った理由の一つだったと思います。父をはじめとした、工場で働く人たちから感じられる「ものづくりは楽しい」という姿はとても魅力的でした。その頃は1階が工場で2階が住居という形だったので、私にとっても現場はとても身近な存在で、工場という現場が近くにあったことが現在の私を支える一つだったと思います。そういう意味では、いつもワクワクしていました。
その後、業務の拡充に伴って、同じ横浜市の金沢区鳥浜町へと工場を移転しました。
私自身は2代目の社長となります。会社としては、父が掲げていたことをさらに発展させて、『お客様に必要とされる会社であり続けたい』というモットーのもと、金型メーカーとして培った技術を活かして、「金型部門」、「プレス・板金部門」、「機械加工部門」、「治工具・設備部門」の4つの柱でお客様の様々なニーズに応えられるような体制をつくって対応しています。
企業理念は、
・お客様にとって頼りになるパートナー企業として満足と信頼を提供し続ける
・働く 1 人ひとりが、やりがいと幸せを実感できる企業を目指す
・より高いレベルの技術を目指し、常に新しい事へのチャレンジをし続ける
という精神のもと、幅広い技術でものづくりをサポートいたします。
少し、4つの柱についてご説明したいと思います。
まず、創業期から中心だった「金型部門」です。
金型については、高品質・高精度の単発型をはじめ、コンパウンド型、順送型、深絞り型など、様々な金型の設計への対応が可能です。もちろん、納品後についてのメンテナンスもしっかりと行っています。
次に「プレス・板金部門」です。
プレスマシンについては、30 トンから 200 トンまでを保有していますので、各種プレス加工への対応が可能です。板金加工については、タレットパンチプレスやレーザーマシン、様々なサイズのベンディングマシンも設備していますので、量産品から多品種少量生産への対応も可能です。もちろん、タッピングなどの後工程から溶接加工まで一貫した生産にも対応いたします。
「機械加工部門」ですが、当社では 3 次元 CAD を導入していますので、設計から実加工までの対応が可能です。金型製造で培った技術を活かしたワイヤー放電加工から、マシニングセンターによる加工、NC 旋盤・研削盤による加工、難加工材を使った加工までを高精度に対応することができます。
最後に「治工具・設備部門」です。
各種加工における治工具の設計から製造、組立て、調整までを行います。この分野には何よりも独自のアイデアや経験が活かされます。当社のもっとも得意とする分野と言えます。
以上のように加工分野が広いため、生産品目は自動車部品から照明機器、産業用機械部品や各種試作品など、お客様のご要望に応じて対応しています。
「プレス・板金部門」に限って言えば、中心となっている材料は、SPCC、SECC、SS400が中心です。板厚としては 2.8~3.2mm までの中厚板が多いですね。
Q.藤澤社長の経歴と 2 代目に就任される際のことをお聞かせください。
先ほども少しお話しましたが、私は子供の頃から父のものづくりの現場の近くで育ってきました。そういう環境でしたから、最初から大学も理工系へと進み、横浜国立大学 機械工学課へと進みました。卒業と同時に、ニッパツ(日本発条)へと就職し、その後 1997 年 11 月にニットーに入社しました。
その後、ニットーにとっても大きな転換期を迎えることになります。
当社にとって大きな転換期となったのはグループ化、現在で言うところの M&A でした。
4 年間の間に、実に 3 社をグループ化しました。
最初に 2004 年に伏見製作所をグループ化。続けて 2005 年に、田辺製作所と資本提携・業務提携を行い行いました。その後 2008 年には小池慎一製作所をグループ会社としています。3 社をグループ化することで、工場の設備などを現在の本社工場に一本化し、体制の強化を図っています。
私自身は、2000 年に専務となり、このグループ化を推進した訳ですが、実は最初はこのグループ化にはあまり乗り気ではありませんでした。しかし結果として、ここで得られた効果はたくさんありました。グループ化するにあたり、それぞれのケースや理由は違いますが、まずメリットがかなり大きい。単純に考えても、4つのメリットがありました。
まず、「雇用の維持」。それぞれの会社には技術を持つ人材がいましたから、そういう意味では短期間で技術を持つ人材を確保できました。
次に「取引先の確保」。各社の取引先をそのまま引き継ぐことができたので、当時の取引先にとっても当社にとってもお互いに安心を得ることができました。
そして「シナジー効果」です。実は、それぞれの会社の持つ技術が少し違っていました。これは取引先が異なることで、それぞれ対象としていた産業が異なっていたからなのですが、これがお互いに良い刺激となり、吸収しあうことができる相乗効果となりました。
最後にこれらを合わせたものですが「新規参入の実現」です。取引先が広がり、本来新規参入が難しい分野へも参入ができました。同時に相乗効果により技術力もアップすることができたので、これまでの取引先にも新しい技術による提案が可能になりました。
この集大成として、2010 年には現在の工場に本社を移転するとともに、すべての会社を移転して、企画管理・生産体制・技術分野のすべてを集約することができました。
Q.設備がかなり豊富ですが、そのあたりをお聞かせください。
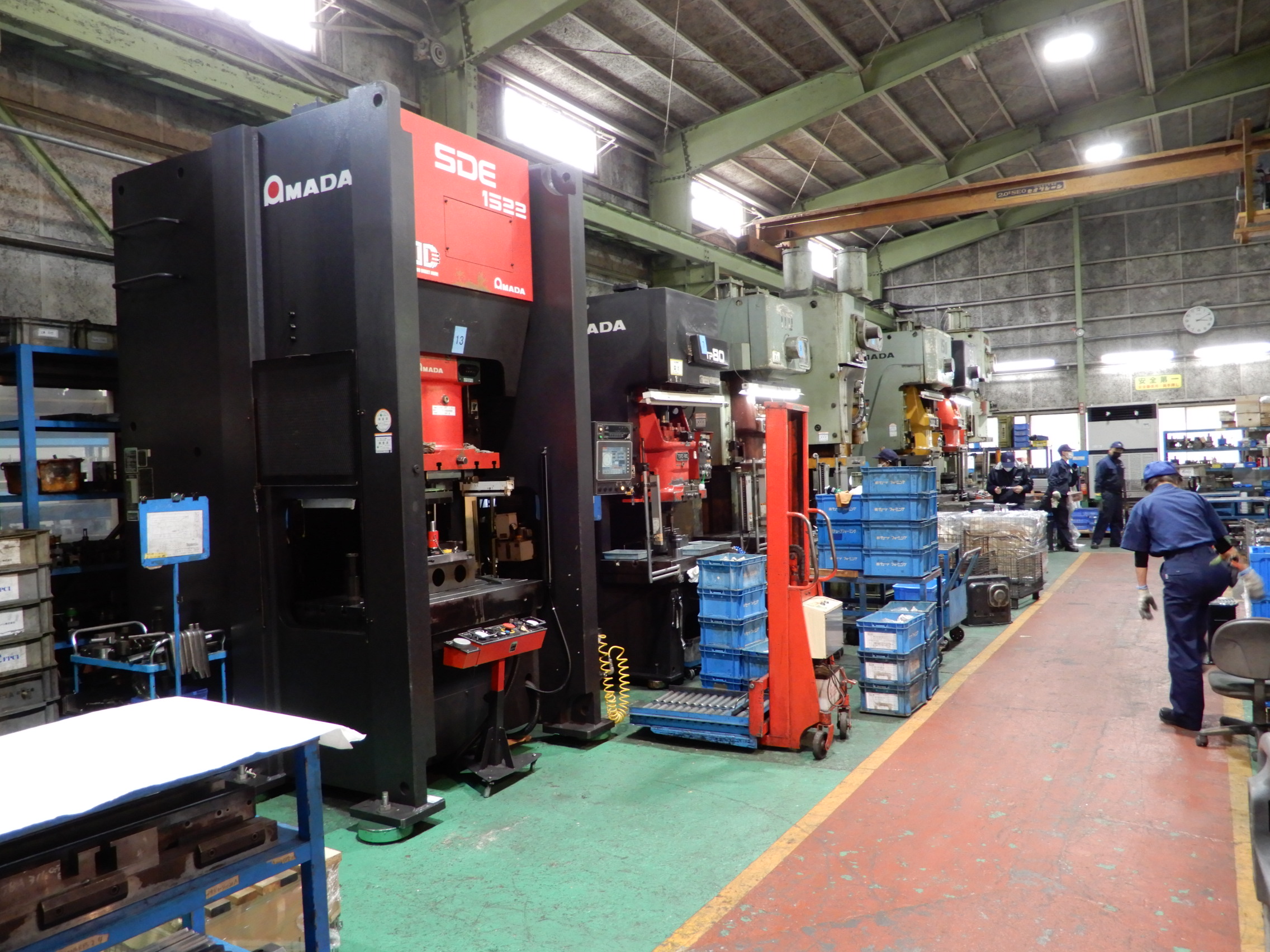
充実したプレスマシン群
やはり、プレス金型からスタートしていますので、プレスマシンの設備については充実していると思います。25 トンクラスから 200 トンクラスまで、16 台のプレスマシンを設備しています。
また板金加工では、ベンディングマシンにも力を入れています。曲げ加工は、板金加工においてもっとも精度が左右される工程なので、差別化ができる技術だと考えています。
それとやはりマシニングセンターですね。当社ではヤマザキマザック製のマシンを加工の目的別に竪型・横型・システムアップなどのマシンを導入しています。機械加工についての経験則が高いのも当社の特長の一つです。特に設計に導入している 3 次元 CAD による設計では、部品の設計だけではなくデザイン面からの検証も行っており、デザインから部品加工までを一貫生産できるというのも強みとなっています。
その他にも、プレス金型の加工には欠かせないワイヤー放電加工機の設備ももちろん、旋盤や研削盤、板金加工のブランク工程では、NC タレットパンチプレスやファイバーレーザーマシン、タッピングなどの中間工程から溶接加工まで、本当に幅広く設備しています。
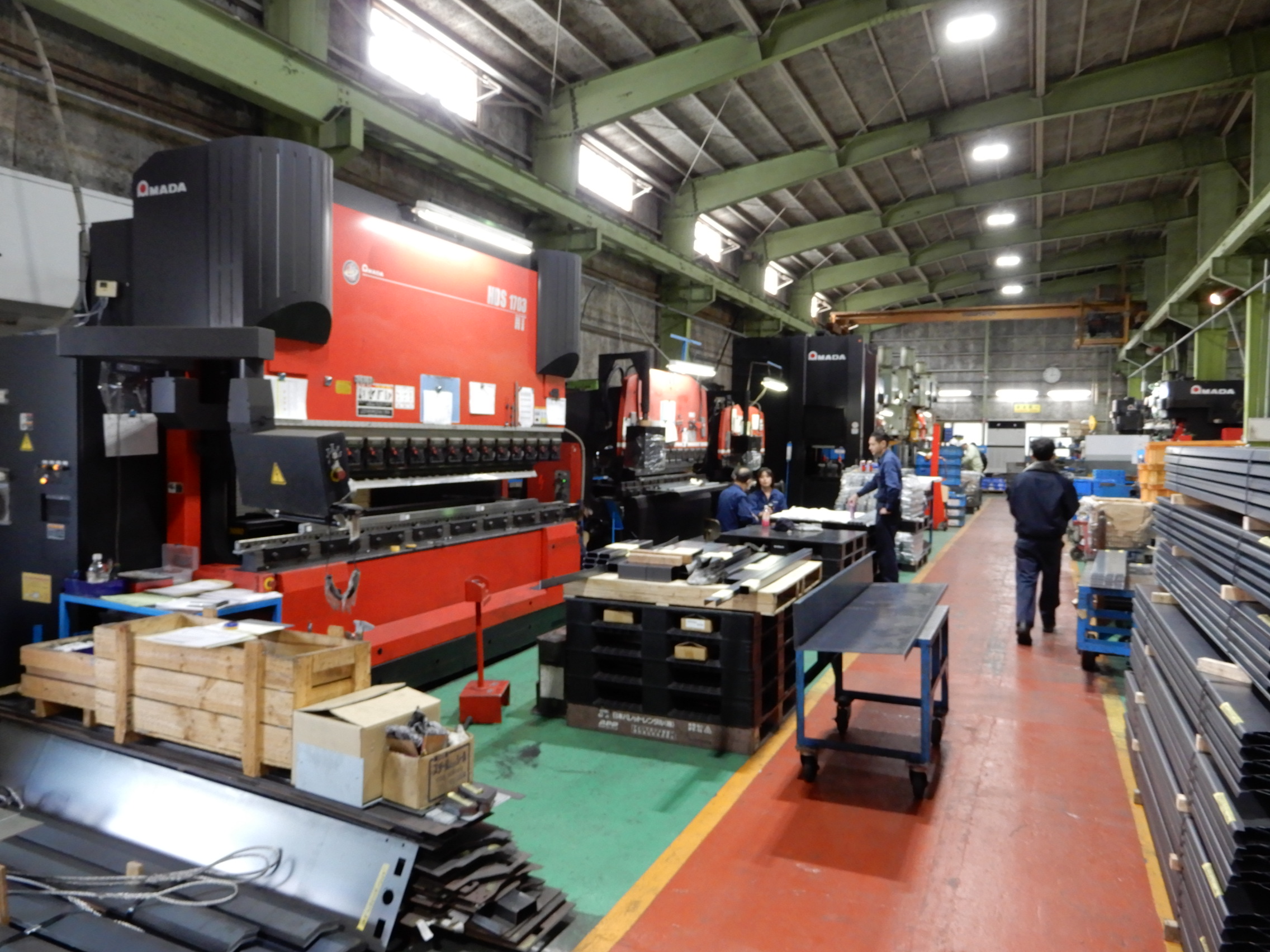
サイズ豊富なベンディングマシン
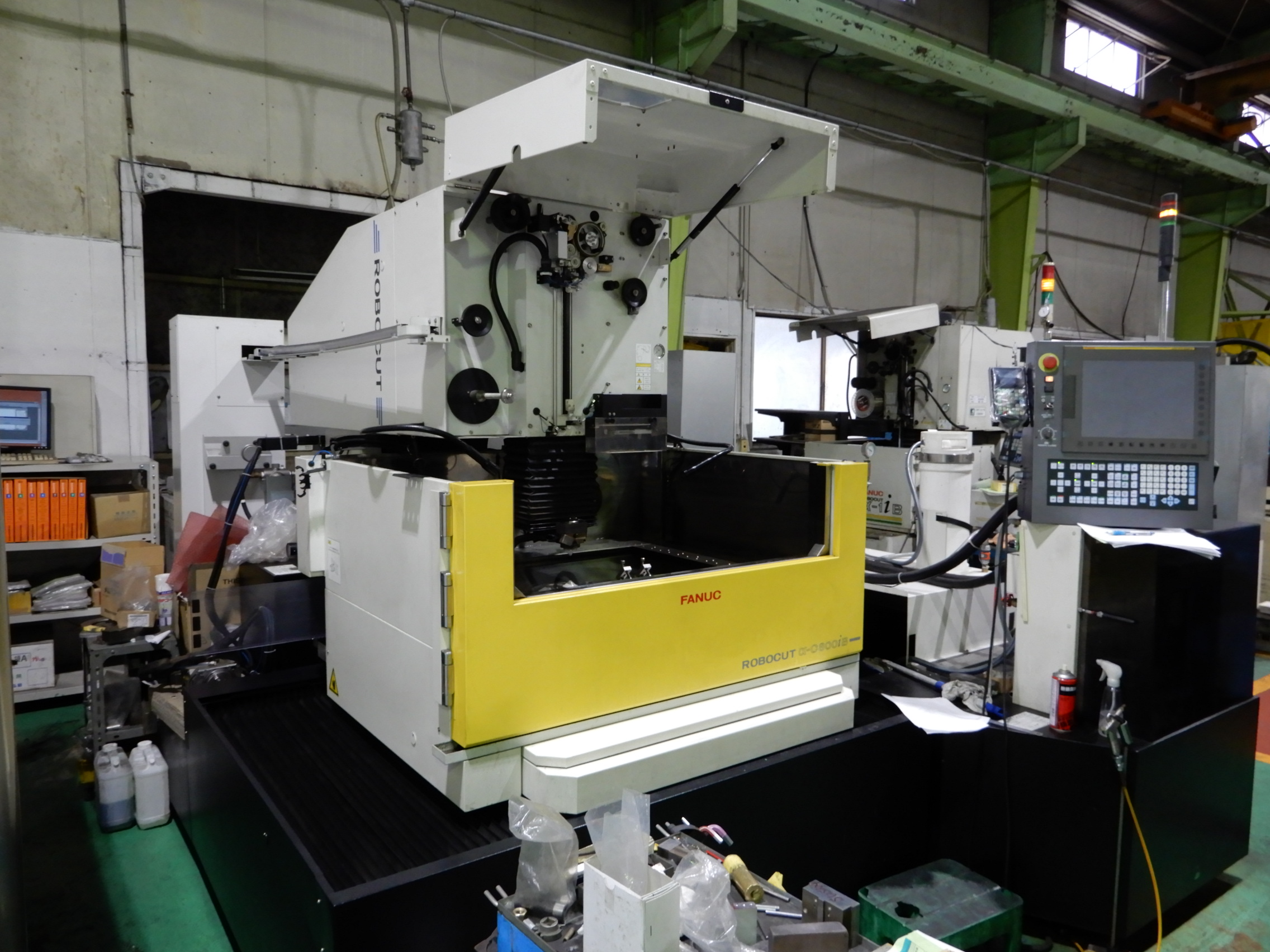
ワイヤー放電加工機
Q.2代目に就任される際のことをお聞かせください。
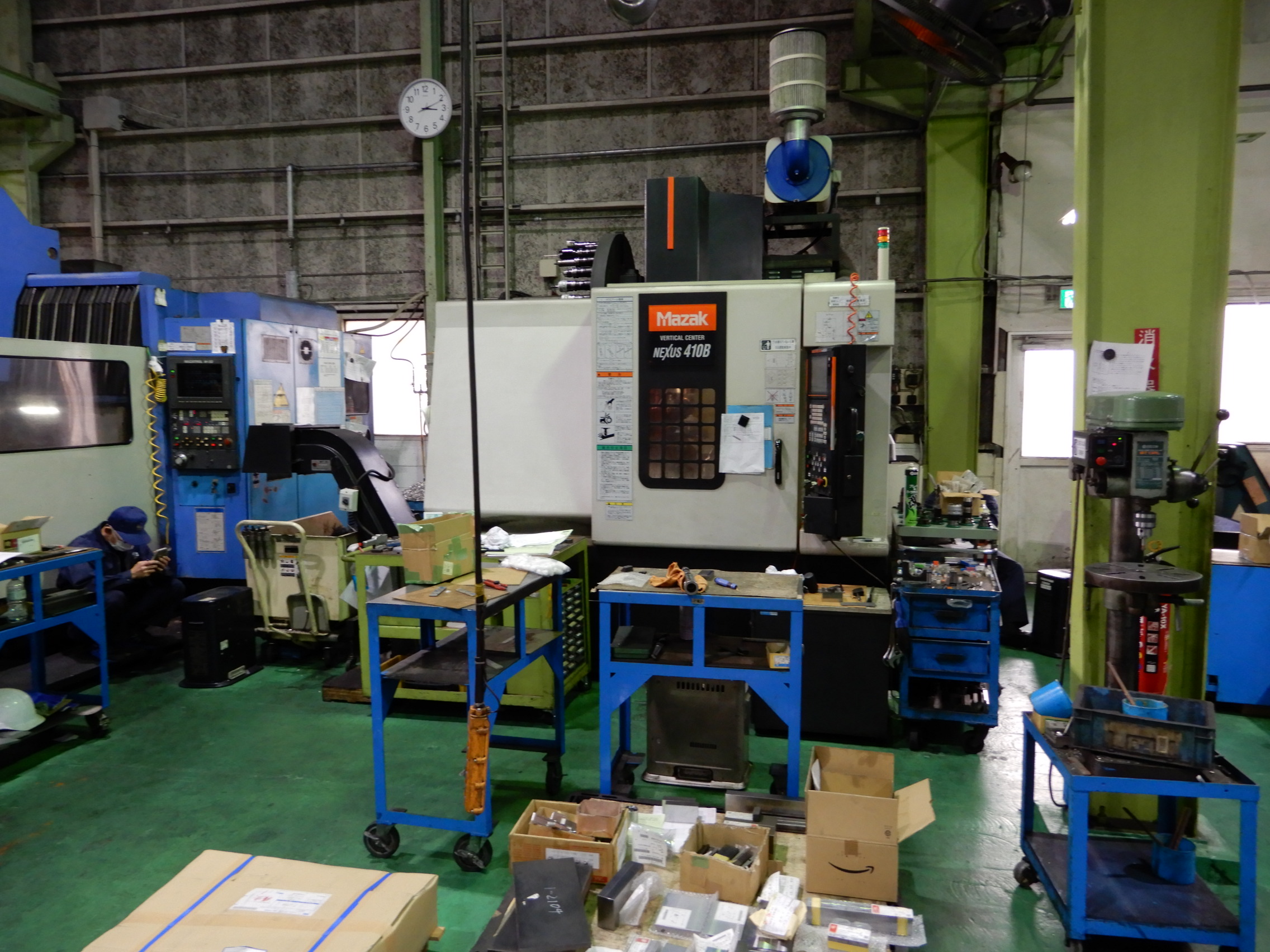
マシニング工程
私自身は、ニットーに入った時から、いつかは父の後を継ぐことになるという認識を持っていました。ですが、不安がなかったわけではありません。
社外で社会人としての経験を積んで戻ってきたわけですが、最初はかなり苦労もしました。当時は私より社歴も長く、現場で実際にものをつくってきた職人さんがたくさんいたわけですから、いくら社長である父の息子だからと言って、途中で入ってきた若造が簡単に通用するものではないですよね。そんな中でも、私自身は「気がついたことは自分からきちんと伝えていこう」と考え、そこは強い気持ちで臨みました。だからこそ、本当に現場をよく回って、コミュニケーションを取り続けながら、一つ一つの工程を丁寧に理解していきました。そんな状況を、社長だった父が無理に後押しをするというのではなく、見守ってくれていたのだと思います。
そんな中で、私はいくつかの提案を始めました。最初は、現場の3S の徹底からだったと思います。製造現場では、3S(「整理」「整頓」「清掃」)は基本ですが、最初のころはきちんとできていない部分もあり、危ない場所もありました。こういう提案は、どちらかというと現場にとっては面倒くさく感じる部分もあります。ですが、この私の提案の後押しをしてくれたのが当時の工場長でした。私は小さい頃から工場に出入りしていましたので、工場長も良く知っていて、とても可愛がっていただいた記憶があります。この工場長が、私の提案を否定することなく、「よし。みんな、まずはやってみよう」と言って、率先して動き始めてくれた。この最初の一押しは本当にありがたかったです。
この後押しで、現場のみんなが動き出してくれました。実際に動きだすと「なるほど。3Sは確かに重要だし、やることで効果があるな。」とみんなが必要性を認めてくれます。
こうした最初の動きから、私が父からバトンを受け継ぐための環境を、みんなが整えてくれたと思っています。私自身は、こういう人の想いやつながりに恵まれていたと感じていますし、当時の工場長には今でもとても感謝しています。
あとは、2000 年に専務に就任した後の4社のグループ化の際に、それぞれ会社の特徴や文化も異なる会社をグループ化するということで、当時とことん皆で話し合ったという経緯がありましたので、当社の中にはみんなが納得できるまで話あうという文化ができていたということも基盤としてありましたので、土台ができていたことも良かったと思います。
Q.社長になられてからは、どういうことに注力されてきたのでしょうか?
私が取り組んだことは、大きく2つありました。一つは「知名度の向上」。そしてもう一つは「エンジニアリング力の強化」です。
まず「知名度の向上」についてですが、当社を知ってもらうためにはどうしたら良いかということについて改めて考えてみました。当社のことを知ってもらわなければ、仕事は広がっていかないということ。そのための私自身の活動をどうするか。最初は、様々なコミュニティに積極的に参加していきました。企業の主催するセミナー的なものから、各団体への参加、さらには地域のコミュニティへの参加などもありました。
当社にとっての強みとして、発注元に話をする時に「うちは何でもできます」と言うのはアピールになりませんでした。自社の技術をアピールするには「差別化」できる技術を説明する必要があります。そこで、目指したのは「尖る」ということ。自社の技術をアピールするためにも、自社でできる技術を駆使したものづくりを行っていこうと考えました。また、当時としてはかなり早かったと思いますが、SNS を使ってこの技術を発表していくことにしました。
このタイミングともう一つの「エンジニアリング力の強化」を合わせて考えたとところ、当社にはもともと一貫生産を始めたとした多彩な技術はあったので、もっと「尖った」ことを発信していこうと考えました。そこで誕生したのが自社製品第一号となる「ヌンチャク系スマートフォンカバー Trick Cover (トリックカバー)」です。これは遊び心から生まれたのですが、自由に回転・移動させることができるカバーがあれば面白いんじゃないかという、そんなことがきっかけでした。試作カバーを作り SNS で発信したところ、すごい数の問合せがありました。当時、製造業としてはまだなかったと思うのですが、クラウドファンディングで資金も集まり、2012 年の発売以降、現在まで世界 43 カ国で 50,000 台の出荷となり、当社の知名度向上にとても役立ちました。
このスマートフォンカバーがきっかけとなり、自社製品やコラボレーション活動などを活発化しています。デザイナーとのコラボレーションや、「YOKOHAMA MAKERS VILLAGE」での活動、そして自社製品であるアシストスーツ「archelis(アルケリス)」へとつながっていったわけです。
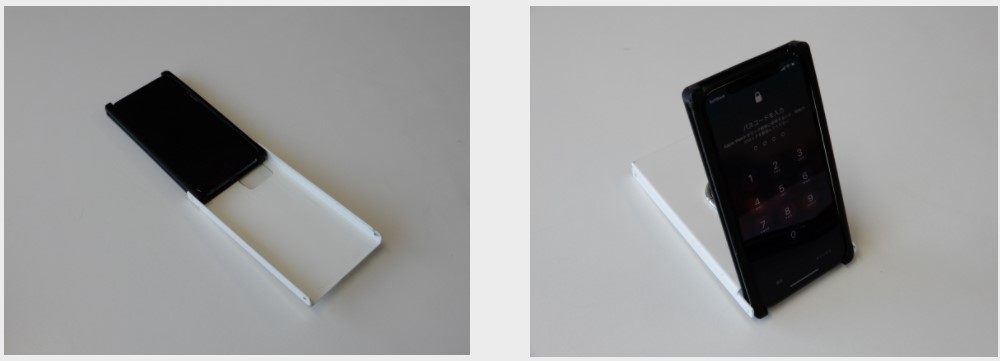
オリジナルスマートフォンカバー『Trick cover』
Q.社員の方々の年齢構成と教育方法について教えてください。
最初に当社がグループ化を図った 2004 年頃は、ニットーは 12 名、伏見製作所が 10 名くらいの従業員数でした。これが現在の従業員数は 50 名、平均年齢は 35 歳となりました。
従業員には海外の人材も活用しており、インド、バングラディッシュ、韓国の人にも働いてもらっています。
これは当社の柱となっている指針なんですが、リーマンショック後に製造業がどんどん海外に拠点を移したり、海外進出を進めていた時期がありました。当社にもそういう話はあったのですが、その時に決めたのは「ニットーは海外への進出はしない。今現在の仲間を大切にして、この横浜の地でやっていく」ということです。これは、リストラなどによって一人も解雇せずにやっていくという宣言でもありました。当然、苦しい時期もありましたが、これを進めていくためには前述の「エンジニアリング力の強化」が重要であるということを再認識したということでもあります。
では、具体的にどうしたか。これは「強み」を活かして「差別化できる技術」により、価格競争に陥らない力をつけていくということに他ありません。製造業である以上、下請けとしての仕事があるため、この仕事に応えていくことは必要ですが、下請け体質となってしまうことは絶対にいけない。そういう考え方になってしまっては、その姿勢が染みついてしまうので新しい発想が生まれない。そうして進めてきたのが、一貫生産という受注方式です。
大手企業では社内に設計ノウハウが残りにくく、アウトソーシングをしたいという相談がいくつかありました。当社では、これまで蓄積してきたノウハウを活かせば、これらの相談に対応できるという自信があったので、こういったケースへの対応が増えていき、「ニットーでなければできない」と言われる仕事、つまり一貫生産として依頼される仕事を増やしていくことができたというわけです。
これまでの実績から考えた時に、ものづくりには幅広い知識と経験が必要であると考えています。一貫生産という考えからもわかるように、自分の関わる部分だけわかれば良いということではありません。当社では、現場では幅広く技術を習得してもらうことを目的に、多能工を目指した教育を行っています。新卒の採用においても、3つの事業部(金型部門、プレス・板金部門、機械加工部門)を経験してもらうような教育体制をとっています。
Q.藤澤社長がこれから目指そうとしていることを教えてください。
私がニットーに入り、現場を見て思ったことの一つとして「職人の意識」ということがあります。私たちのようなものづくりの現場は、依頼された仕事を当たり前に毎日こなしていきます。仕事を受けて、その製品をつくる。職人にとってはこれが当たり前のことです。そのため、職人は技術のレベルについて考えなくなってしまう。慣れによって勘違いしてしまうわけです。実は、知識と経験に裏付けされた、とてもレベルの高い仕事をしているにも関わらず、それを特別だと思っていないんです。この経験と知識に裏打ちされた技術を、きちんと認めて認識できる環境をつくっていきたいと考えています。
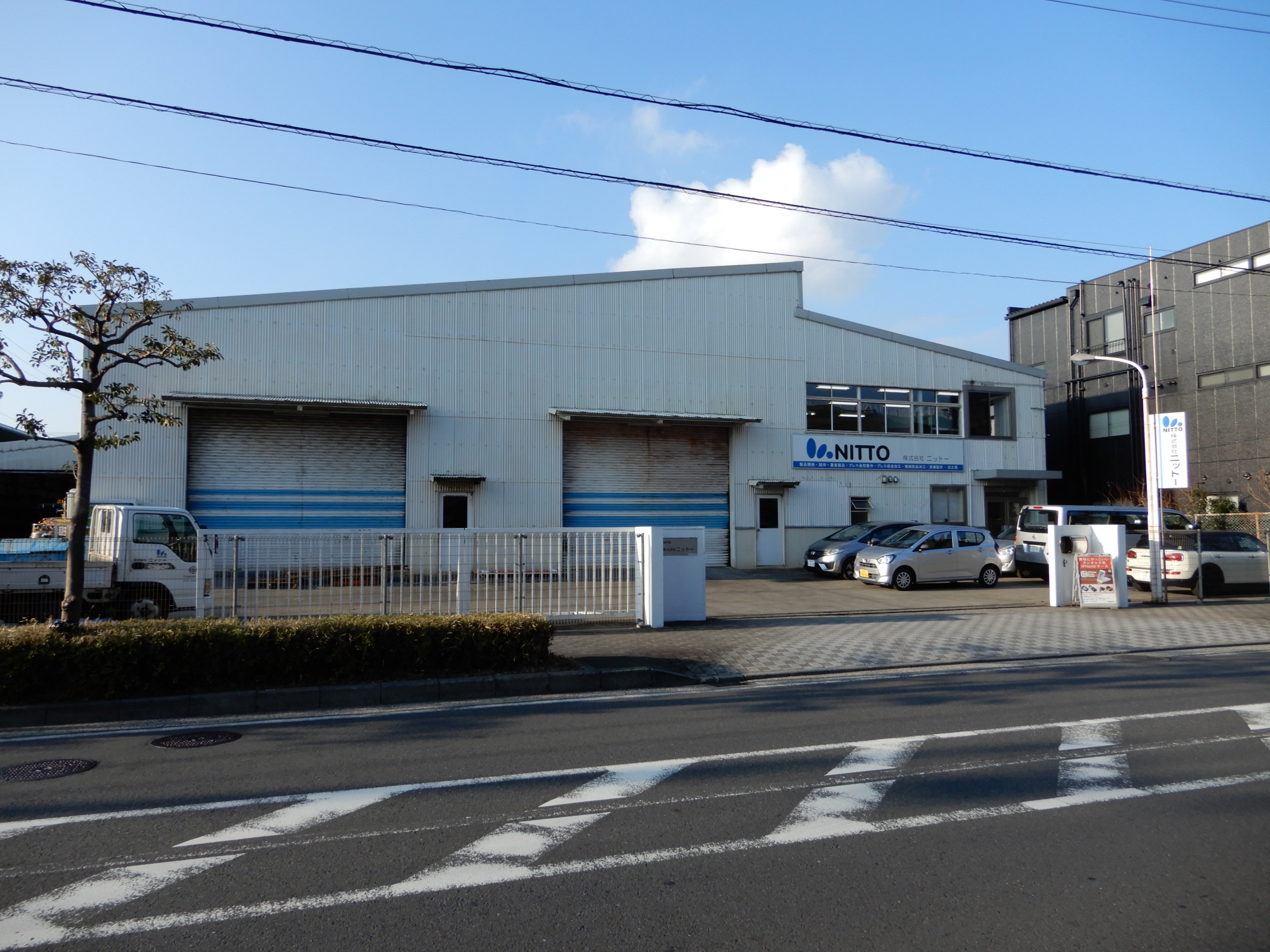
社屋外観
ただし、改めなければならないこともあります。日本の製造業全体に言えることかもしれませんが、例えば 1,000 個の生産ができる金型製作の依頼があったとしても、数万個の加工が可能なレベルの金型を製造してしまう。これは明らかにオーバースペックで、日本ではこれが当たり前に行われている傾向があります。これではコスト面では折り合わなくなってしまうので、その目的に合わせた最適な製品をつくっていく。つまり「最適な技術」を提案できることが大切だと思っています。
それともう一つ。常に差別化技術をリードしていくということ。
現代は、様々なことがすごいスピードで進んでいます。ものづくりの現場も例外ではありません。当社のような金属加工で培ってきた技術が、いきなり全く新しい技術が生まれた時に置き換わってしまう可能性もある。突然、価値がなくなってしまうということが起こるかもしれないわけです。どういう状況でも対応できる体制を整えておくように考えておくことが大切だと思います。
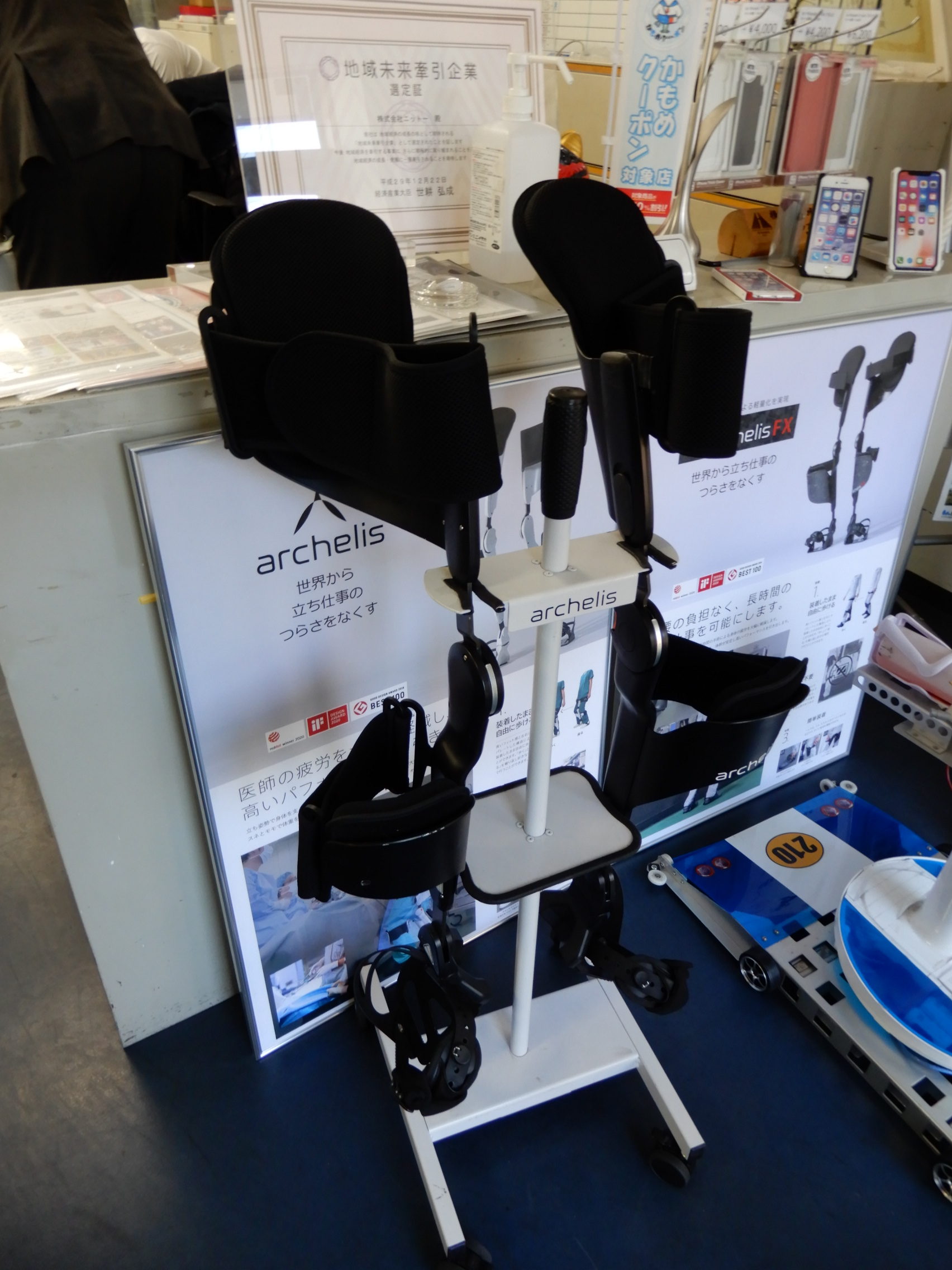
archelis(アルケリス)
その一つの方向性として、当社で開発した「archelis(アルケリス)」があります。
2018 年に産学連携という形で開発した「archelis(アルケリス)」は、最初は自治医科大学の川平医師からの「長時間立った姿勢で手術をする医師の身体的負担を軽減できないか」という相談からスタートしました。当社の知識と技術力を活かし、試行錯誤を繰り返しながら、「装着しながら移動することもでき、しかも電源が不要なアシストスーツ」の開発に成功しました。今後はさらに様々な用途への活用に展開していきます。
本来、ものづくりは楽しいことです。こうした活動から、私たちの技術でこれからも社会に役立つ有意義な企業を目指していきたいと考えています。
ありがとうございました。
株式会社ニットー 会社情報
【沿革】
1967 年 神奈川県横浜市磯子区岡村町に日東工業を創立
1968 年 有限会社ニットウに法人改組
1978 年 横浜市金沢区鳥浜町へ工場移転
1992 年 株式会社ニットーに社名変更
2004 年 有限会社伏見製作所をグループ会社とする
2005 年 有限会社田辺製作所より資本・業務提携を行い、グループ会社とする
2006 年 有限会社伏見製作所を吸収合併し、同社を株式会社ニットー朝比奈工場として開設
2008 年 有限会社小池慎一製作所をグループ会社とする
2010 年 新本社工場を設け、朝比奈工場と小池慎一製作所を新本社工場へ移転
2013 年 第 30 回神奈川工業技術開発大賞ビジネス賞 受賞
2013 年 第2回素形材連携経営賞素形材センター会長賞 受賞
2017 年 平成 28 年度神奈川県優良工場 認定
2017 年 経済産業省 はばたく中小企業 300 社 認定
2017 年 経済産業省「地域未来牽引企業」に認定
2020 年 「archelis(アルケリス)」の仕組みが日本工業規格 JIS 化される
2020 年 アルケリス株式会社をグループ会社として設立
当初、金型メーカーとして設立し、そこから「プレス金型」「プレス・板金加工」「機械加工」「治工具・設備」の4つの業務を主軸として展開。
『お客様に必要とされる会社であり続けたい』というモットーのもと、幅広い技術であらゆるニーズへのものづくりにチャレンジを続けている。
自社で開発したアルケリスは、装着することで足腰への負担を軽減することができるアシストスーツとして注目されている。従業員は 50 名
株式会社ニットーのホームページはこちら